橡膠廢氣處理 橡膠廢氣處理設備 廢氣治理洗滌塔 活性炭吸附凈化除臭裝置 活性炭吸附除臭設備 光催化除臭設備 光氧催化廢氣處理裝置 UV光解凈化器設備
橡膠廢氣處理對焊教程:安全高效連接之道
在橡膠廢氣處理系統中,管道的連接至關重要,而對焊技術以其牢固、密封性***的***點被廣泛應用。本教程將詳細講解橡膠廢氣處理管道的對焊操作步驟、要點及注意事項,助力實現安全、高效的焊接作業。
一、焊接準備
1. 材料與工具
管道材料:選用符合橡膠廢氣處理工況要求的管材,如 PP(聚丙烯)、PVC(聚氯乙烯)等塑料管材,確保其具有******的化學穩定性和耐腐蝕性。檢查管材外觀,應無裂縫、變形、老化等缺陷,管壁厚度均勻。
焊接設備:準備專業的塑料管道熱熔對焊機,包括加熱板、銑刀、液壓站(或手動夾具)等組件。確保設備運行正常,加熱板溫度控制精準,銑刀鋒利且切削平整。
輔助工具:干凈柔軟的布用于擦拭管道表面;量尺、標記筆用于測量和標記管道;安全防護用品如護目鏡、手套、工作服等必不可少。
2. 工作環境
選擇通風******、干燥、無塵的室內空間進行焊接作業,避免陽光直射和潮濕環境影響焊接質量。清理工作區域,移除易燃物、雜物,保持地面整潔,防止絆倒。
確保電源穩定供應,電壓波動范圍應在設備允許范圍內,避免因電壓不穩造成焊接參數變化。
二、管道切割與清潔
1. 切割管道
根據設計圖紙和實際安裝需求,使用專用管道切割刀具(如旋轉切刀)垂直于管道軸線進行切割,保證切口平整、光滑,無毛刺。切割后的管道端面應與管道軸線垂直度偏差不超過±5°。
對于***口徑管道,可采用鋸弓配合鋸條進行初步切割,再用砂輪機打磨切口,使其達到平整光滑的要求。切割過程中注意不要使管道內部產生過多碎屑,如有可用壓縮空氣吹凈。
2. 清潔管道
用干凈柔軟的布蘸取適量酒精或丙酮,徹底擦拭管道切割面及外表面,去除油污、灰塵、水分等雜質。確保清潔后的管道表面光亮、無污漬殘留,這對于提高焊接質量和焊縫強度至關重要。
清潔后的管道應及時進行焊接,若長時間暴露在空氣中,需重新清潔后再施焊,以防止雜質再次附著。
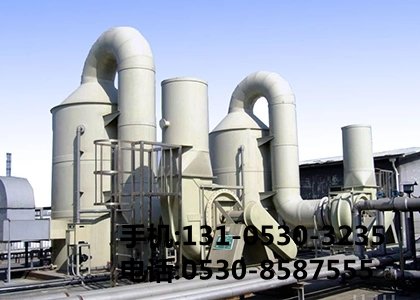
三、對焊操作流程
1. 固定管道
將待焊接的兩根管道分別水平放置在焊接支架上,調整管道位置,使兩管道同軸度偏差控制在±0.5mm 以內,可通過在管道下方墊木塊或使用定位夾具來實現***對齊。
使用液壓站(或手動夾具)將管道兩端固定牢固,施加適當的夾緊力,防止焊接過程中管道移位。夾緊力***小應根據管道規格和材質確定,一般以不使管道產生明顯變形為宜。
2. 銑削管端
啟動銑刀,將其置于兩管道對接端面之間,緩慢進給銑刀,同時沿管道軸線方向往復移動銑刀,均勻銑削出約 0.5 1mm 厚的翻邊。銑削過程中要保持穩定的速度和壓力,確保翻邊尺寸一致、表面平整,不得有溝槽、振紋等缺陷。
銑削完成后,迅速抽出銑刀,用刷子清除管道內殘留的碎屑,并用干凈的布擦拭翻邊表面,保持清潔。
3. 加熱板材
根據管道材質和規格,設定加熱板的加熱溫度和時間。一般來說,PP 管材加熱溫度在 210 240℃,加熱時間約為 10 30 秒;PVC 管材加熱溫度在 160 200℃,加熱時間約 8 20 秒。開啟加熱板電源,待溫度升至設定值后,讓加熱板恒溫一段時間,確保溫度均勻分布。
加熱板表面應保持清潔、平整,若有污垢或損傷,應及時清理或更換,以免影響加熱效果和焊接質量。
4. 對接加熱
將加熱后的加熱板迅速插入兩管道翻邊中間,使加熱板與管道翻邊充分接觸,保持一定的壓力(一般為 0.5 1MPa),開始計時加熱。加熱過程中要確保加熱板與管道貼合緊密,不得有晃動或間隙。
加熱時間根據管道壁厚、材質等因素確定,通常為管材壁厚的 10 15 倍(秒)。例如,對于 10mm 壁厚的 PP 管道,加熱時間約為 100 150 秒。加熱完成后,按照加熱板放入的逆序緩慢取出加熱板,避免刮傷翻邊。
5. 切換對接
在加熱板取出后,立即將兩根管道的翻邊對準,快速平穩地將管道合攏,使兩翻邊緊密結合。合攏過程中要嚴格控制管道的同軸度和錯邊量,一般同軸度誤差不超過±0.2mm,錯邊量不***于管道壁厚的 10%。
同時施加適當的軸向壓力(約為 0.2 0.5MPa),并保持一定時間(約 30 60 秒),使焊縫處受熱均勻,冷卻固化。在保壓冷卻期間,嚴禁移動管道或在管道上施加外力,防止焊縫開裂。
6. 冷卻定型
焊接完成后,讓管道自然冷卻至室溫。冷卻時間根據環境溫度、管道材質和尺寸而定,一般不少于 30 分鐘。在冷卻過程中,要保持管道處于靜止狀態,避免外界因素干擾焊縫的凝固和結晶。
四、焊接質量檢驗
1. 外觀檢查
冷卻后的焊縫應平整光滑,無氣孔、裂紋、夾雜、飛邊等缺陷。焊縫寬度應均勻一致,與母材過渡自然。用肉眼觀察焊縫表面顏色,正常焊縫顏色應與母材相近或略深,若出現焦黃、過淺等異常顏色,可能是焊接溫度過高或過低所致。
測量焊縫高度和寬度,焊縫高度一般為管材壁厚的 0.5 1 倍,寬度應覆蓋整個翻邊寬度,且均勻對稱。對于不符合要求的外觀缺陷,應及時標記并采取補救措施,如打磨修整或重新焊接。
2. 尺寸檢測
使用量具測量焊接后的管道同軸度和橢圓度。同軸度偏差應控制在±0.2mm 以內,橢圓度不得超過管道外徑的 2%。若尺寸偏差超出標準范圍,可能是焊接過程中管道固定不穩或受力不均造成的,需分析原因并進行調整修復。
檢查管道長度是否符合設計要求,若有誤差應控制在允許范圍內。對于需要***安裝的管道系統,還需對法蘭接口、支吊架安裝位置等關鍵尺寸進行復核。
3. 壓力測試
在外觀和尺寸檢驗合格后,進行壓力測試以檢驗焊縫的密封性和強度。采用氣壓試驗或水壓試驗方法,試驗壓力一般為工作壓力的 1.25 1.5 倍,穩壓時間不少于 30 分鐘。在試驗過程中,仔細觀察焊縫及管道各部位有無滲漏現象,若有泄漏則判定焊接不合格,需查找漏點并進行返工處理。
壓力測試合格后,緩慢排放試驗介質,拆除試驗裝置,并對管道進行全面檢查和清理,確保無殘留介質和雜物。
五、常見問題及解決方法
1. 焊接過程中出現冒煙現象
原因:可能是焊接溫度過高,導致塑料管材分解產生煙霧;或是加熱板與管道接觸不緊密,局部過熱引起冒煙。
解決方法:降低加熱板溫度至合適范圍;檢查并調整加熱板與管道的貼合度,確保均勻受熱。若已產生冒煙,應立即停止焊接,清理冒煙部位并重新進行焊接操作。
2. 焊縫出現氣孔
原因:加熱板加熱時間過短或溫度不夠,使得塑料未能充分熔化融合;管道端面清潔不徹底,存在油污、水分等雜質;焊接過程中受到外界氣流干擾。
解決方法:適當延長加熱時間或提高加熱溫度;加強管道端面的清潔工作;在焊接區域設置防護屏障,減少空氣流動對焊接的影響。若氣孔較小且不影響整體性能,可在焊縫冷卻后進行補焊修復;若氣孔嚴重,則需割除有問題的焊縫部分,重新進行焊接。
3. 焊接完成后管道變形
原因:焊接時夾緊力過***或加熱時間過長,造成管道內部應力集中;管道冷卻過程中未均勻收縮,受到外力約束。
解決方法:調整夾緊力至合適數值,嚴格控制加熱時間和溫度;在冷卻階段采取自然冷卻方式,避免強制冷卻或快速降溫。若管道已發生輕微變形,可嘗試在變形部位進行局部加熱矯正;若變形嚴重無法修復,則需更換新的管道重新焊接。
通過以上對橡膠廢氣處理管道對焊教程的詳細闡述,希望能夠幫助操作人員熟練掌握對焊技術,確保橡膠廢氣處理系統的管道連接安全可靠、密封嚴實,從而有效保障廢氣處理工作的順利進行。在實際焊接作業中,要嚴格遵守操作規程,注重每一個環節的細節把控,不斷積累經驗,及時發現并解決問題,以提升焊接質量和工作效率。